Kingston startup Cyclic Materials has started working with global electric car company Polestar to build a closed loop recycling pathway for the rare earth elements (REEs) that help give electric motors a low environmental footprint.
“We’re hoping that we can replace all of the virgin REEs with recycled REEs,” said Sandor Johilo, circularity lead with Polestar, a Swedish automotive brand established in 1996 by Volvo Cars’ partner Flash/Polestar Racing and acquired in 2015 by Volvo, which itself was acquired by Geely in 2010. Polestar had revenues of $1.3 billion US in 2021.
While Polestar cars are manufactured in China and REEs are mostly mined in that country, recycling REEs is still less harmful to the environment than using virgin REEs. Plus, according to Johilo, shipping has a lower environmental footprint than most people think.
OBJ360 (Sponsored)
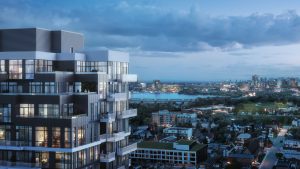
Parkdale Collective: Hintonburg’s new curated rental living by Richcraft
In the ever-evolving pulse of central Ottawa, something bold, fresh and creative is emerging. Parkdale Collective is more than a place to live – it’s a lifestyle destination for those
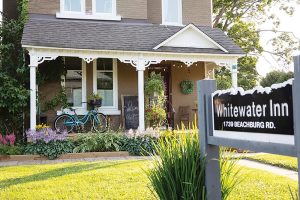
Your next memorable getaway awaits in Whitewater Region
If you’re eager to immerse yourself in some quintessentially Canadian experiences, look no further than Whitewater Region in the County of Renfrew, in the Upper Ottawa Valley. It’s a four-season
“We have done life cycle assessments and assessments for shipping a lot of things. While shipping as a sector globally does have a big carbon footprint, in terms of shipping certain components to China from other parts outside of China or the cars from China to the markets, it’s actually smaller than expected,” said Johilo.
The relationship between Polestar and Cyclic Materials will also be circular, with Polestar purchasing recycled REEs from Cyclic and the latter recycling Polestar cars that contain REEs.
“Cyclic Materials will not make the magnets for us, they will just provide the raw materials for the magnet,” said Johilo. “From Cyclic Materials, the REEs will go to around two suppliers before becoming a magnet and then, once that magnet is made, it goes to a supplier who puts it into a motor and then that motor is supplied to us,” explained Johilo. “At the end of life, it’s just one step — the dismantler is between us and Cyclic at the end.”
When EOBJ spoke with Cyclic Materials in October 2022, the company was working on its pilot.
“We finished the pilot; we targeted 75 kg of output and produced 105 kg and processed more than 280 kg of feed material, which was basically 20 per cent more than we expected,” said Ahmad Ghahreman, CEO of Cyclic Materials.
Having completed the pilot at Kingston Process Metallurgy, Cyclic Materials has been able to parlay that success into interest from potential customers, including Polestar. The next step is to establish what Ghahreman calls the “North American mesh.”
“We are building our first commercial spoke and hub in Kingston but beyond that we will have five spokes in North America — U.S. and Canada — and one larger hub in Canada and that will be our North American plan,” said Ghahreman. He explained that the spokes collect the magnets that Cyclic can process and hubs take the magnet waste and turn it into the product that’s sold to the likes of Polestar.
“It was quite fortunate that (Cyclic) found us and then approached us and it just happened to be that we were super-excited and interested in this solution,” said Johilo. He added that while the mass of the magnet in a car is small, it punches above its weight in terms of biodiversity and raw material footprint from mining and processing. “It’s in the top two of most environmentally impactful parts of the car.”
However, there is still some testing to do to prove that Cyclic Materials’ product is uncontaminated with impurities.
“It has been questioned by some colleagues — that if it’s recycled material it doesn’t have the same quality of performance — so there are people and organizations that are claiming they do not want to have 100 per cent recycled REEs because it’s going to be lower quality,” said Johilo.
Cyclic Materials is not worried. “What we’re producing is of a higher purity than what comes out of most mine operations,” said Patrick Nee, co-founder and vice-president of strategic partnerships at Cyclic Materials.
According to Nee, the confusion arises from a process called magnet-to-magnet recycling.
“That’s a little bit like taking a loaf of bread and saying we’re going to return that bread to dough and we’re going to make another loaf of bread out of that dough. But the crust is still in there, so you won’t get quite as good a second loaf of bread. What we at Cyclic Materials are doing is taking that loaf of bread and recycling it back to flour. The flour is as good as the original flour and you can make cookies or pizza or a different loaf of bread,” explained Nee.