With no construction experience to speak of, Dutch immigrant Arie Daalder has parlayed a passion for craftsmanship into a $1.2-million business building custom bunkies, cabins, cottages and log homes.
In 2007, Daalder was looking for a more sustainable career. An aunt in the Netherlands suggested he try building bunkies as a business.
“I have been self-employed all my life, so I was comfortable with the business side, but I had no construction experience. I knew how to hold a hammer, but I didn’t always hit the nail square on the head,” he admits. “Then I started researching, putting things together, trying a few little things and one day everything fell into place for me.”
OBJ360 (Sponsored)
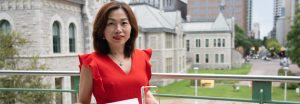
Care, Serve, & Give: Dr. Helen Tang is redefining what it means to lead with purpose
Dr. Helen Tang is a dynamic and multifaceted leader whose passion for community and philanthropy is at the heart of everything she does. As a devoted mother of two and
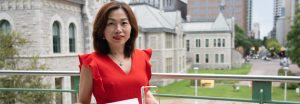
Care, Serve, & Give: Dr. Helen Tang is redefining what it means to lead with purpose
Dr. Helen Tang is a dynamic and multifaceted leader whose passion for community and philanthropy is at the heart of everything she does. As a devoted mother of two and
With a keen desire to learn and a cousin in construction in the Netherlands who acted as a willing if distant mentor, Daalder opened his first workshop in his garage in Avonmore, Ont., southeast of Ottawa.
“I just started out with something very basic … and now over time it’s expanded into larger buildings and even log homes,” says Daalder, who started with structures of about 100 square feet.
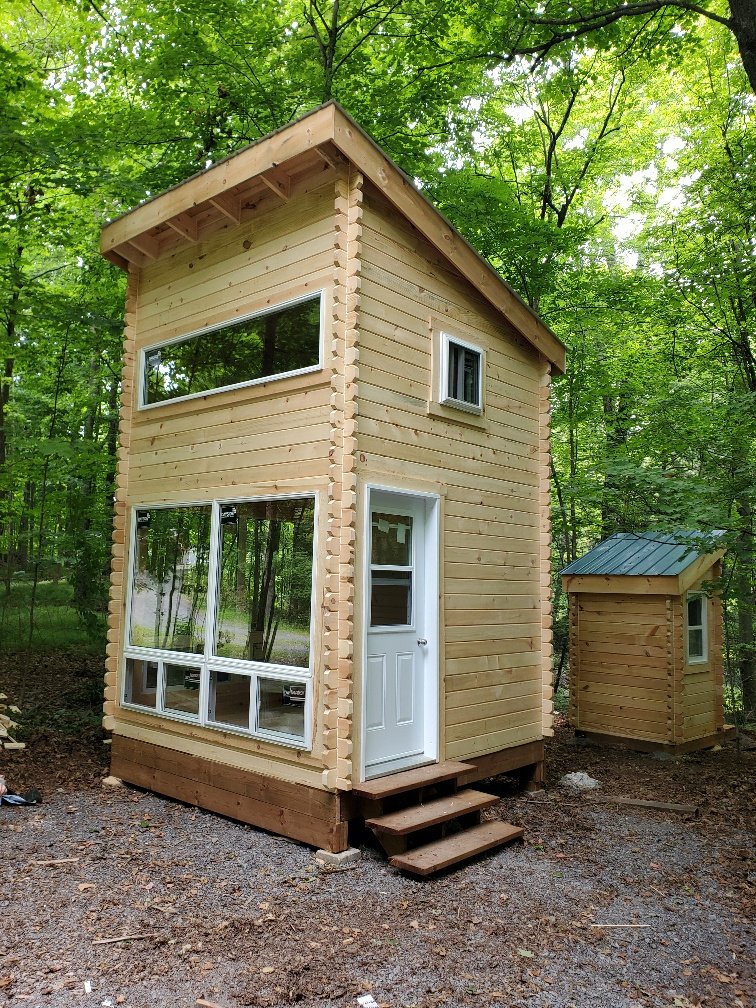
It took Daalder a few years to get up and running with Custom by Arie. He says his biggest challenge was finding a suitable lumber supplier.
“I wanted a supplier who could do everything for me — supply the lumber as well as mill it for me. I don’t remember how I found my current supplier, but I went to meet them and everything fell into place,” says Daalder.
About five years ago, Daalder moved his operation to a 6,500-square-foot warehouse in Winchester, not far down the road. He puts in 10- to 14-hour days most of the year. On larger full-service builds he sometimes hires local help, but he still does most of the work himself, only outsourcing his accounting and social media.
“I’m a very hands-on kind of guy. When a customer calls with a question or a problem, I can solve it over the phone or Facetime. I like the technical part of the business. I enjoy the building,” he says.
However, the business has taken some unexpected turns.
“The business went in a totally different direction than what I anticipated,” he says. “I found there is a niche market in the cottage space for structures of 100 square feet to five and 600 hundred square feet. I ended up tapping into that space by accident.”
In the Netherlands, he explains, bunkies are used as backyard sheds or out-buildings for small gatherings and Daalder expected a similar appetite in Canada. His current business is for three-season buildings, but he is noticing another shift in the market.
“There is a bit of a trend out there that people want to convert their bunkies into four-season buildings over time,” says Daalder, who finds out what the client’s long-term plans are and designs accordingly. “If they’re converting to four-season after two or three years, we’re already set up with an insulated foundation and with insulated windows and doors.”
He’ll also build tiny homes and says, while he gets a lot of inquiries about them, it isn’t translating into a lot of demand.
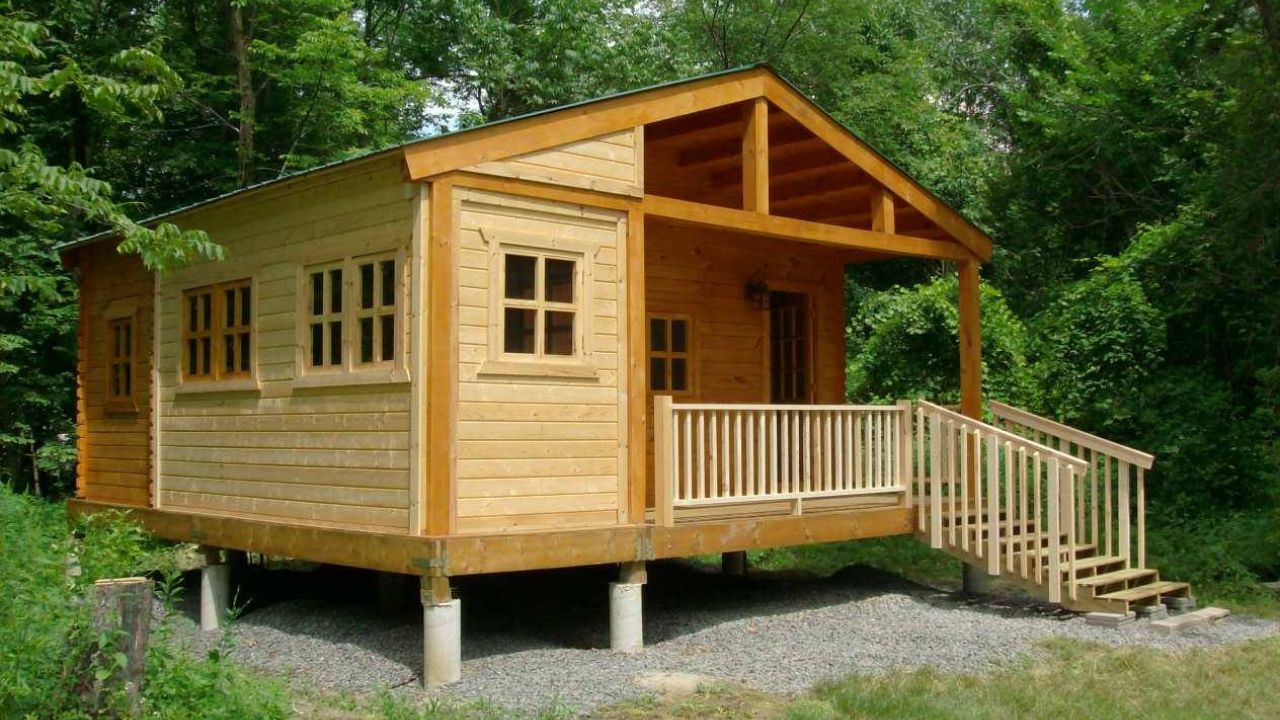
“There is a bit of a problem because it costs about $300 per square foot to build a house and that cost is still the same for tiny homes. People are just not aware yet of the cost involved, so it can be a bit of a challenge,” says Daalder. Another barrier, he says, is that a lot of municipalities haven’t worked out the regulations around tiny houses and that can complicate permits.
Daalder’s customers range from southern and northern Ontario, to Manitoba, Quebec and British Columbia.
“Right now, I’m in the process of pre-fabricating two bunkies to be built on Vancouver Island,” he says. “These are 14 by 14 with a full second floor, so we make three big crates and every crate has a different part of the bunkie and then we close it up and ship it out.”
The kits are packaged with numbered instructions for easy assembly and include windows, doors and all the fasteners and hardware needed to complete the project.